A sewing & embroidery blog
Recent posts
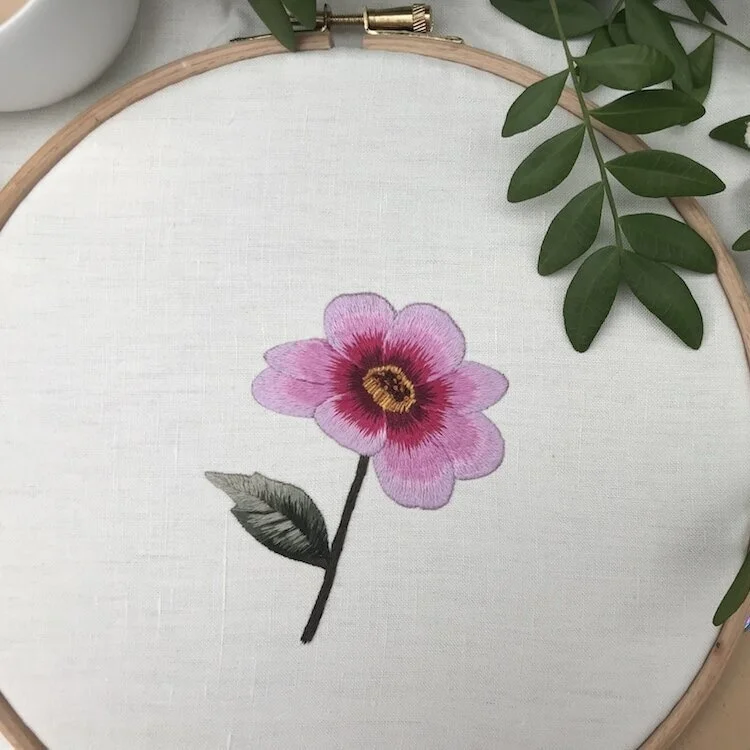
Embroidery
Silk Shaded Dahlia
Embroidery
Embroidery
Sewn Wardrobe
Tutorials